新卒採用で知っておくべき自動車用語:フルモデルチェンジとは
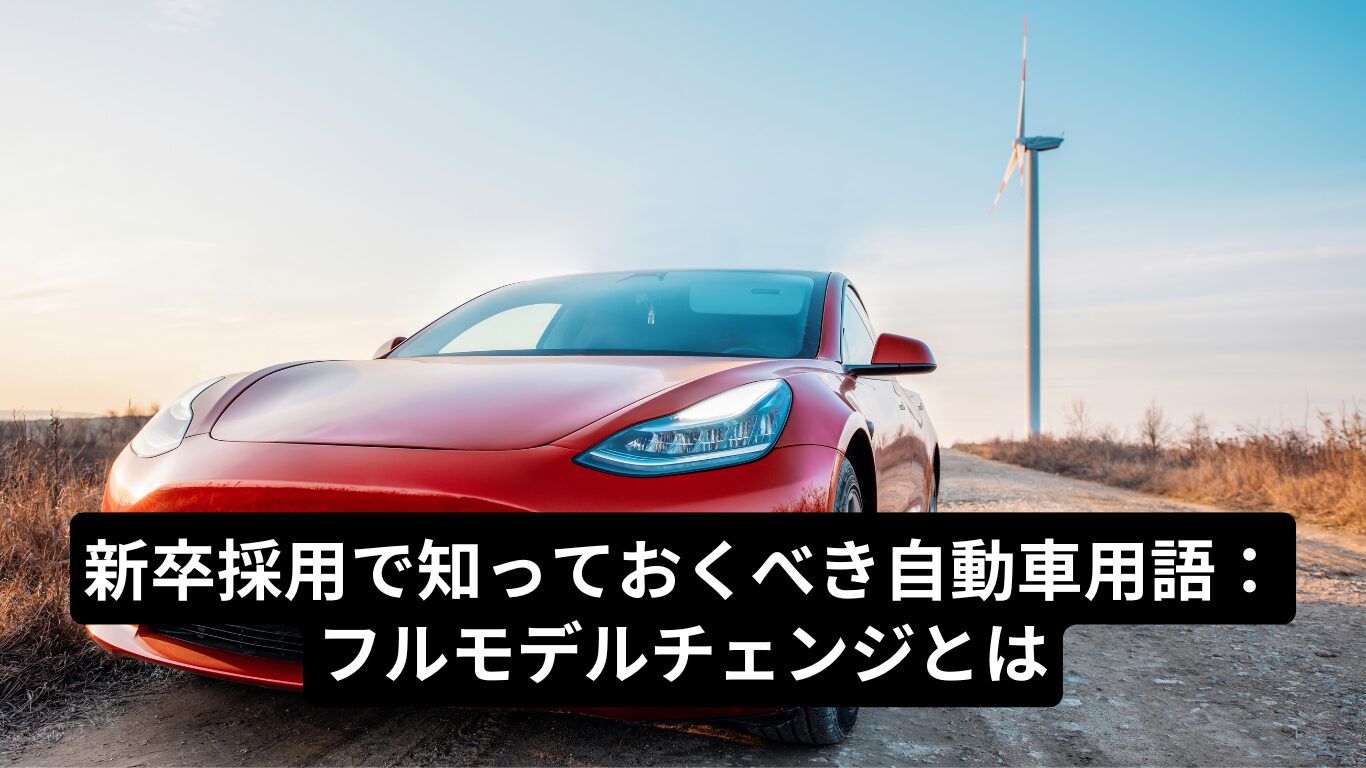
新卒の学生及び中途の求職者により広く詳しく轟自動車のことを知ってもらうために、会社説明資料(採用ピッチ資料)をご用意しています。下記リンクをクリックしてダウンロードしてください。
→ 轟自動車の会社説明資料をダウンロード
はじめに
自動車業界の就職活動では、商品開発に関する質問が頻出です。とりわけフルモデルチェンジは、メーカーの技術力と経営戦略が凝縮された一大プロジェクトとして、面接でよく話題に上がります。
このプロジェクトは、企画から開発、生産準備まで、数年にわたる大規模な取り組みです。自動車メーカーの総合力が試される重要な機会であり、成功すれば市場での競争力を大きく高められる一方、失敗すれば経営に深刻な影響を及ぼすリスクもあります。
この記事では、就活生の皆さんが知っておくべきフルモデルチェンジの基礎知識から最新の開発手法まで、分かりやすく解説していきます。面接対策はもちろん、入社後の業務理解にも役立つ内容となっています。
フルモデルチェンジの基本概念
定義と目的
フルモデルチェンジとは、車両を基本から作り直す全面改良を指します。外観デザインの刷新はもちろん、プラットフォーム(車台)やパワートレインなど、基本構造から見直しを行います。
目的は、時代の要請に応える新しい価値の創造です。環境性能や安全性能の向上、デザインの刷新、快適性の改善など、複数の目標を同時に達成することが求められます。製品の競争力を維持・向上させる上で、不可欠な取り組みとなっています。
開発サイクル
一般的な開発サイクルは4〜6年です。この周期は、技術革新のスピード、市場動向、開発投資の回収、生産設備の償却などを総合的に考慮して決定されます。
開発期間は通常36〜48ヶ月程度で、この間に商品企画、デザイン開発、技術開発、生産準備などの工程が進められます。近年は開発期間の短縮が課題となっており、デジタル技術の活用などにより、効率化が図られています。
投資規模
フルモデルチェンジには、数百億円から数千億円規模の投資が必要です。この投資には、開発費用、金型費用、生産設備の更新費用などが含まれます。
投資の回収計画は、プロジェクトの重要な要素です。販売台数予測に基づき、適切な価格設定と収益計画を立案する必要があります。投資効率の最大化は、開発段階から重要なテーマとなっています。
マイナーチェンジとの違い
マイナーチェンジは、基本構造を維持したままの部分改良です。一方、フルモデルチェンジは基本構造から見直す全面改良となります。投資規模や開発期間にも大きな違いがあります。
マイナーチェンジは通常、フルモデルチェンジの中間時期に実施され、商品力の維持・向上を図ります。外観の一部変更や、装備の充実などが主な内容となります。
商品企画プロセス
マーケティング調査
商品企画の第一段階は、綿密なマーケティング調査です。市場動向、顧客ニーズ、競合状況など、様々な角度から情報を収集・分析します。
最近は、ビッグデータやAIを活用した調査手法も導入されています。SNSでの評価分析や、実走行データの解析など、新しい手法による深い洞察が可能になっています。
顧客ニーズの分析
収集したデータを基に、顧客のニーズを詳細に分析します。現行モデルのユーザー評価、改善要望、潜在的なニーズなど、多面的な分析が行われます。
世代別、地域別、使用目的別など、様々な切り口での分析により、ターゲット層の明確化と、それに応じた商品性の設定を行います。
コンセプト立案
分析結果を基に、新型車のコンセプトを立案します。デザイン、走行性能、環境性能、安全性能など、様々な要素について目標を設定します。
コンセプトは、開発の指針となる重要な要素です。プロジェクト全体を通じて、このコンセプトに基づいた一貫性のある開発が求められます。
競合車分析
競合車の徹底的な分析も重要なプロセスです。性能、品質、価格などあらゆる面での比較検討を行い、新型車の目標設定に反映させます。
ベンチマーク車両の選定から始まり、性能測定、分解調査など、詳細な分析が行われます。この結果は、開発目標の設定に活用されます。
技術開発の流れ
プラットフォーム開発
プラットフォームは、車両の基本骨格となる重要な要素です。剛性、軽量化、衝突安全性など、様々な要求性能を高次元で両立させる必要があります。
最近は、複数の車種で共通のプラットフォームを使用する傾向が強まっています。開発効率の向上とコスト削減を図りつつ、各車種の特性に合わせた最適化を行います。
パワートレイン計画
エンジンやトランスミッションなど、パワートレインの開発は重要な要素です。環境規制への対応と、走行性能の向上を両立させる必要があります。
電動化への対応が重要なテーマとなっており、ハイブリッドシステムや電気自動車用のパワートレインなど、新技術の開発が活発に行われています。
安全技術の革新
衝突安全性能の向上や、予防安全システムの開発など、安全技術の革新は重要なテーマです。法規制の強化への対応と、市場要求の高まりに応える必要があります。
自動運転技術の開発も進んでおり、センサー技術や制御技術の進化により、より高度な安全システムの実現が可能になっています。
環境性能の向上
CO2排出量の削減や、燃費性能の向上など、環境性能の向上は必須の課題です。パワートレインの効率向上、軽量化、空力性能の改善など、総合的なアプローチが必要です。
材料技術の進歩により、軽量化と強度向上の両立が可能になっています。空力解析技術の発達により、より効率的な形状の開発も進んでいます。
デザイン開発プロセス
エクステリアデザイン
外観デザインは、顧客の購買意欲に直結する重要な要素です。ブランドアイデンティティの表現と、時代性の両立が求められます。最初のアイデアスケッチから、クレイモデル、デジタルモデリングを経て、最終デザインが決定されます。
空力性能や歩行者保護などの技術要件と、デザイン性の両立が重要な課題です。3次元CADシステムの活用により、デザインと機能の早期検証が可能になっています。
インテリアデザイン
室内空間のデザインは、使い勝手と快適性が重視されます。操作性、視認性、材質感など、様々な要素を考慮しながら開発が進められます。
最近は、デジタル化への対応が重要テーマとなっています。大型ディスプレイの配置や、ユーザーインターフェースのデザインなど、新しい要素が加わっています。
カラーデザイン
外板色や内装色の開発は、商品性を左右する重要な要素です。トレンド分析や市場調査を基に、新色の開発が行われます。
塗装工程での実現性や、長期耐久性なども考慮する必要があります。環境に配慮した水性塗料の採用など、技術面での革新も進んでいます。
デジタルモデリング
3次元CADを活用したデジタルモデリングにより、開発効率が大きく向上しています。デザインレビューや性能評価を、実物を作る前に行うことが可能になっています。
バーチャルリアリティ技術の活用により、より実践的な評価が可能になっています。設計部門との早期連携も容易になり、開発期間の短縮に貢献しています。
生産準備と品質管理
製造ラインの準備
新型車の生産に向けて、製造ラインの改造や新設が行われます。既存ラインの改造では、現行モデルの生産と新型の準備を並行して進める必要があります。
自動化設備の導入や、作業性の改善など、様々な取り組みが行われます。作業者の負担軽減と、品質向上の両立を図ります。
部品調達計画
数千点に及ぶ部品の調達計画は、プロジェクトの成否を左右する重要な要素です。サプライヤーとの協力体制を構築し、品質、コスト、納期の最適化を図ります。
新技術の採用による部品の新規開発や、既存部品の改良など、様々な取り組みが必要です。グローバルな調達体制の構築も重要な課題となっています。
品質保証体制
新型車の品質を確保するため、厳密な評価体制が構築されます。部品レベルから完成車まで、様々な段階での品質チェックが行われます。
耐久試験や性能試験など、実車による評価も重要です。市場導入後の品質モニタリング体制も整備されます。
量産体制の確立
試作段階から量産への移行は、重要なプロセスです。品質と生産性を両立させながら、徐々に生産台数を増やしていきます。
作業者の習熟度向上や、設備の調整など、様々な課題に対応する必要があります。安定した品質の確保が最重要課題となります。
開発期間のマネジメント
スケジュール管理
フルモデルチェンジの開発は、通常3〜4年の期間を要します。この長期にわたるプロジェクトのスケジュール管理は、極めて重要です。各工程の進捗管理や、部門間の調整が必要となります。
デジタルツールを活用したプロジェクト管理により、リアルタイムでの進捗確認や、問題点の早期発見が可能になっています。開発の各段階でのマイルストーンを設定し、計画的な推進を図ります。
コスト管理
開発費用、設備投資、部品コストなど、様々な側面でのコスト管理が必要です。目標原価の達成に向けて、設計段階からコストを意識した開発が行われます。
バリューエンジニアリング活動により、不要なコストの削減と、商品価値の向上を両立させる取り組みが行われています。グローバル調達の活用など、コスト競争力の強化も重要なテーマです。
リソース配分
人材、設備、予算などの限られたリソースを、効率的に配分する必要があります。プロジェクトの優先度に応じて、適切な配分を行います。
特に技術者の配置は重要で、専門性と経験を考慮した人材配置が行われます。外部リソースの活用や、グローバルな開発体制の構築なども進められています。
リスク管理
開発期間中の様々なリスクに対する管理体制が必要です。技術的な課題、市場環境の変化、部品調達の問題など、様々なリスクに対応する必要があります。
定期的なリスク評価と対策の立案により、プロジェクトの円滑な推進を図ります。不測の事態に備えた代替案の準備も重要です。
グローバル展開戦略
市場別仕様
各国の法規制や市場ニーズに対応した仕様設定が必要です。安全基準、排出ガス規制、燃費規制など、様々な要件に適合する必要があります。
気候条件や道路状況など、地域特有の環境にも配慮が必要です。これらの要件を満たしながら、開発の効率化とコスト抑制を図ります。
生産拠点の選定
グローバルな生産体制の構築には、各拠点の特性を考慮した戦略が必要です。生産能力、品質レベル、コスト競争力など、様々な要素を評価します。
為替リスクの分散や、現地調達の可能性なども重要な検討要素となります。拠点間の相互補完体制の構築も進められています。
まとめ
フルモデルチェンジは、自動車メーカーの総合力を結集する重要なプロジェクトです。企画、開発、生産準備まで、数年にわたる一貫した取り組みが必要となります。
電動化や自動運転など、新技術への対応が求められる現在、フルモデルチェンジの重要性はますます高まっています。この記事で学んだ知識は、自動車メーカーの面接でも必ず役立つはずです。
商品開発の中核となるフルモデルチェンジについて理解を深めることで、自動車業界でのキャリアを切り開く第一歩となるでしょう。時代の変化に対応しながら、魅力的なクルマを生み出していく—それがフルモデルチェンジの本質なのです。
会社案内資料ダウンロード
当社は創業以来、大切にしている事があります。それは、スタッフが働きやすく成長でき楽しく笑顔で働ける環境づくりです。みんなで協力し、力を合わせて笑顔で働ける環境を築けるようスタッフ同士のふれ合いの場や自分が成長できる学びの場(研修)に力を入れています。
人生の中で、働いている時間はとても大きな割合を占めます。その大きな割合を占める時間を、働きやすく自分が成長できる環境で楽しい仲間と笑顔で働きませんか?